What is Kanban and How is it Useful?
We often hear a lot of lean terms and tools used but have little to no idea what they mean. The specific tool that I will be outlining will be Kanban. So, what is Kanban? The literal definition of Kanban means "signboard." A Kanban system is actually a microsystem of a larger system which is a pull system. It is a common tool used to ensure material gets to the end user at the right moment (Just-in-Time). It identifies three key things:
-
what's needed,
-
when it's needed, and
-
quantity required.
Many people believe the Kanban system developed by Taiichi Ohno, the godfather of the Toyota Production System (TPS), was solely his idea. That is not entirely true. He and his team members were visiting a grocery store in the United States and discovered how they managed inventory and stock control. He soon realized he could adapt the same concept not only in the manufacturing process but in any process that has to manage inventory and productivity. Ohno saw how this would address unnecessary inventory and low levels of productivity and decided to take action.
There's a well-known saying, “choose to use Kanban as a method to drive change in your organization, and you are subscribing to the view that it is better to optimize what already exists because that is easier and faster and will meet with less resistance than running a managed, engineered, name-change initiative. Introducing a radical change is harder than incrementally improving an existing one.” ― David J. Anderson, Kanban.
The Kanban method itself is relatively simple. It consists of a Kanban board which has several cards. Each card visualizes a task present on the board and also describes its progress.
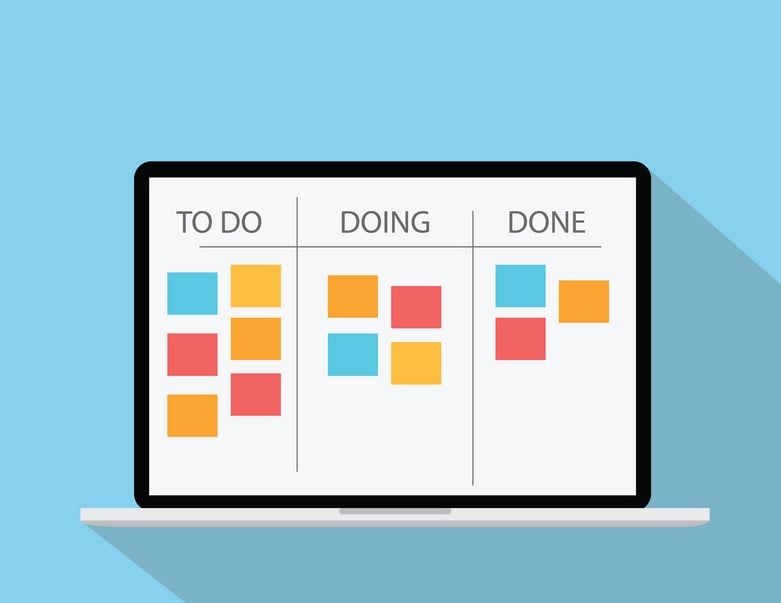
Usually, a card is used to send information to an upstream customer. Then, the card request parts from someone who will pull those specific parts and that specific quantity from a storage location such as a parts supermarket. When parts are consumed, either through the parts supermarket or directly from the downstream process, a certain unit of consumption would trigger a production Kanban card to be sent back to the producing process else would trigger new production.
Here's an illustration of how a Kanban system works (See example A).
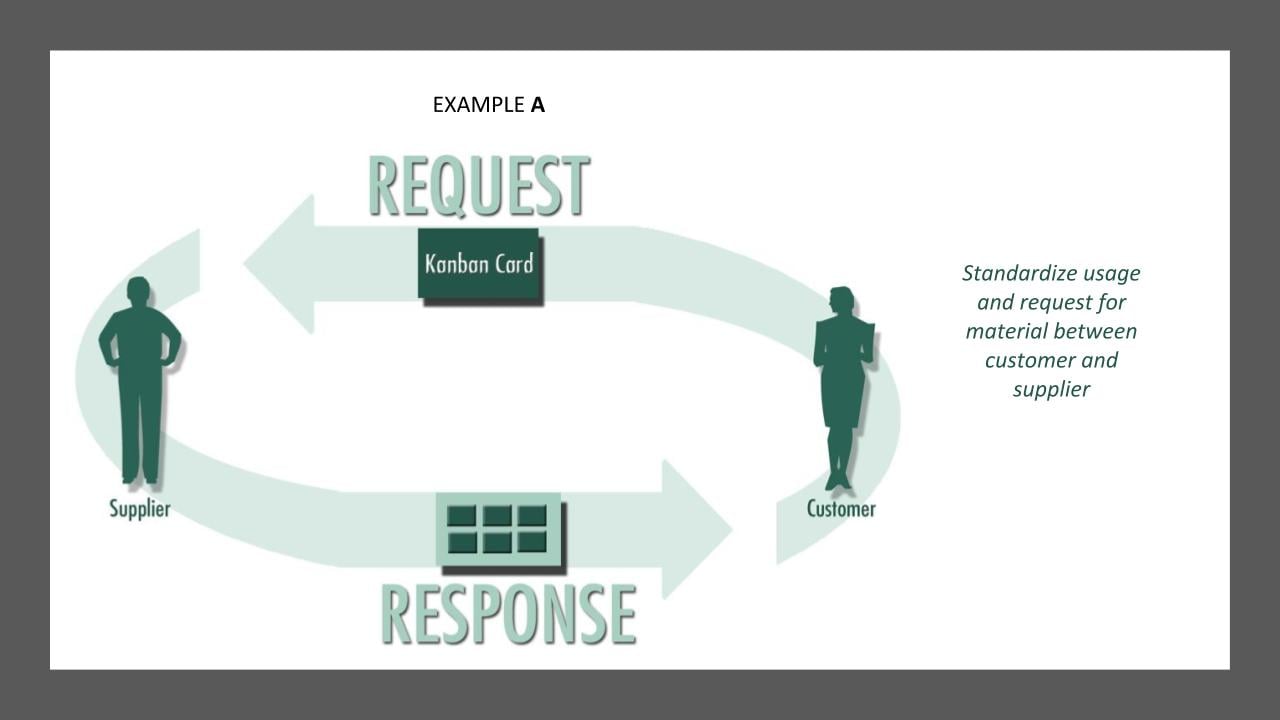
There are several principles that need to be considered when establishing a Kanban system. These are put in place to maintain the integrity of the system. One is, defective parts are not sent to the next process. This would cause significant problems for internal and external customers. Anything that is defective is pulled immediately and sent to a holding area.
The second principle is the downstream process comes to withdraw only what is needed. This is crucial for more than one reason. If you request more than what is required, you throw off the inventory storage balance. If you take more than you can store, you'll have excess material to manage. And, if you send too much material to the next process station, they are not prepared to use it.
The next principle is the upstream process only produces to replenish what was withdrawn. You never take more or less than what is needed. The system is designed for specific quantities for a reason.
The fourth principle is parts must not be produced or delivered when there is no need. You do not produce or get ahead for protection or a buffer. If you deliver parts or produce prematurely, the internal customer isn't ready to produce, receive, or process it.
Another crucial principle is Kanban cards must be attached to the actual parts or container. It's very important that the card stays with the material to eliminate confusion or mistakes. You don't want an operator or employee to memorize or assume what the quantity should be moving forward. That way no matter who processes it or where it is in the process, the quantity will always be specific.
Last but not least, the actual quantity of parts in the container must match the number on the Kanban card. The information must be accurate to be effective. Leaders and operators must conduct regular audits of the process to ensure the supplier delivery quantity and quality is the same or lead times haven't changed.
Here are some common practices for implementing a Pull System (Lean Kanban):
1. Visual management with containers:
Containers or storage units can be used by signaling when to replenish the suppliers or parts. When the container is empty, that signals to the person that it needs to be refilled.
2. Electronic Pull Systems:
Electronic alarms and signaling devices can be used to alert a person that more material or parts are needed in the process. It is also referred to as the "trigger" for action to be taken.
3. Kanban:
It is simply a type of visual management (VM) or a pull system. Kanban methodology is the process of how the system itself works.
4. Supermarkets:
The process in which establishes mini storage locations throughout the production environment. It creates a visual system for managing Work in Progress (WIP). This enables higher utilization of material handling resources by consolidating material storage and delivery (See example B).
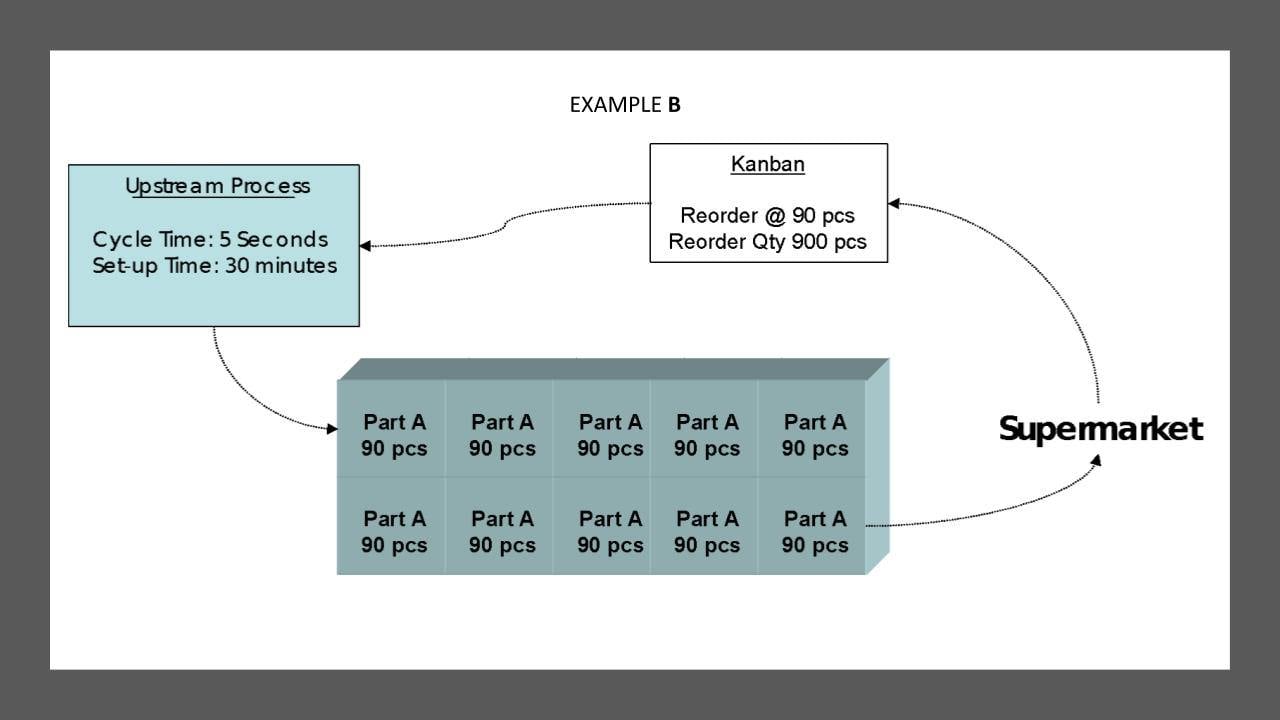
5. Visual Management Inventory (VMI):
This type of pull system is very convenient for managing small parts such as screws, bolts, paper clips, etc. Often, an outside supplier is responsible for visiting the facility on a weekly or prescribed time and refilling the parts as needed. There are many benefits of a Kanban system:
- Clear connect of every customer and supplier:
This is very important to ensure that we are delivering exactly what the internal customer is expecting from us.
- Eliminate waste of inventory:
Excess inventory is very easy to overlook and is often missed. There are many costs to having excess inventory. It’s literally money left on the floor because it's not sold. It creates a huge safety risk for employees. It takes up valuable real-estate that could be used for production.
- Establish high agreement of the quantity and timing of parts delivery:
This is where you have to have a clear connection with not only your internal customers but external as well. The vendor that provides you with the goods and service must know when you need suppliers and how much to deliver to you. The internal customer must know how much to expect and when it is coming from the supplier. If this does not occur, you must contact the vendor immediately for supplies.
- Deviations from the established and acceptable practice are minimized since the signal indicates that there is only one appropriate response:
Kanban methodology is one of my favorite tools for the reason stated earlier. Since the process is clearly defined, there is little to no ambiguity in the process. No one has to guess or "figure out" what to do. The standardized procedure and visual aids defined everything for you.
- Two people or processes can communicate and operate together with the high agreement without working side-by-side:
Since the process is clearly defined, multiple people and the process can operate at the same time without any interference.
Several advantages of a Kanban system:
-
Reduced Inventory: pull systems restrict the amount of Work in Progress (WIP)
-
Shorter Cycle Times: less WIP allows product to flow faster
-
Lower Costs: lower inventory frees working capital
-
Greater Flexibility: production system responds to the environment, not to a predetermined plan
-
Exposes Problems: responsiveness and visualization of the system show weak points in the production processes.
It is clear that Kanban in lean development is a vital tool and proven to be very useful. It is critical to ensure that the people that are most knowledgeable about the part of the workflow or process are charged with identifying an area or system to put a pull system into place. Once that is identified, the following steps need to occur:
-
Find a part or set of parts where pull should be established
-
Determine a technique for requesting material
-
Identify storage location, standard container size, etc.
-
Establish a pull process as an experiment
Make sure Kanban card rules are understood by everyone who touches them. This doesn't need to be perfect. You can make adjustments, as needed, to improve the process. When looking for ways to improve the process, these are the elements that should be considered.
The withdrawal of necessary products with specified quantities at a specific time from the former process should be done by the subsequent process. This former process should produce products for the subsequent process in the quantity that the latter will withdraw. The amount of Kanban cards should be reduced and should be used to change to small changes in demand. If these key and essential elements are in place, you have a very efficient Kanban system.
A Kanban card contains all the needed information for both the request and responder and has the following information (See example C):
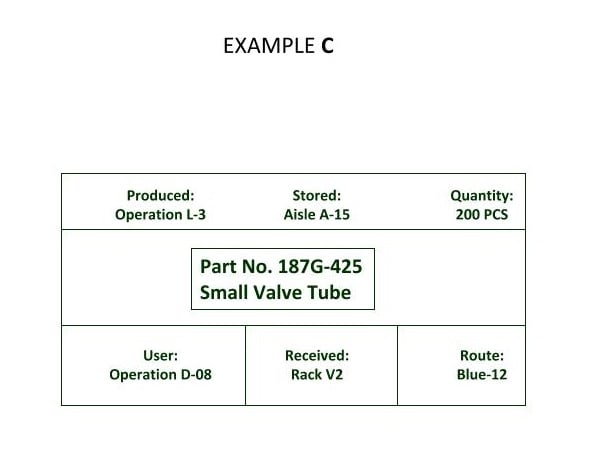
-
Part name or number
-
Quantity per card
-
Location to be picked up or produced
-
Location to be delivered or consumed
-
The number and the total number of cards in the system (i.e. 2 of 6 cards)
In conclusion, a high agreement has to be established as to the meaning of the Kanban signal. Everyone must have a clear understanding of their roles and responsibilities. There must be organizational discipline to comply with Kanban. If people are deviating from the standard, they are creating new or different standards and the system will fail. You must have a continual audit and adjustment of the system. This is to make sure that the system is functioning as intended and the supply and demand are still the same as when it was established.
Looking for a change? Get Lean Six Sigma certified