KAIZEN: How does it aid in Continuous Improvement projects
Kaizen spirit has been present in operations, improvements and transformations under many names including Good-Change, Workout, and Blitz. However, regardless of what it is called, it represents a critical phase in the Total Quality Management field and is utilized in all Continuous Improvement projects. The spirit of Kaizen is a philosophy, a set of tools and a process.
What is Kaizen?
Kaizen is a Philosophy and mindset: The basic principle and creed of this process are that the organization with its leadership and the operations are open to taking a deep look at their current state objectively and are able, willing to change for the better in the future state. Acknowledging that the only thing constant is change, organizations have been using Kaizen to change.
Kaizen plays a critical role in the organization as it provides increased capabilities under the disposal of the Black Belt. The pressure on the Belt leading the Continual Process Improvements effort is mitigated by changing the hearts and minds of all SMEs and Stakeholders to accept that Change is Good.
The Black Belt is tasked with identifying and leading Kaizen projects that focus on achieving the goals of the organization as a whole and at the same time focus on the Line of Business (LOB). Kaizen brings the team into understanding the organization as it sees itself in the industry and where this organization wants to be. This mindset considers the organization’s strengths, weaknesses, opportunities, and threats.
Kaizen scope reaches the core of achieving profitability, which is critical to every organization’s success. This philosophy of Continual Improvement (CI) practices shares the organization’s objectives to maximize profit and minimize cost.
This philosophy and mindset of good change (Kaizen) need to be stronger than the forces of inertia. The basic legacy thinking that “if it’s not broken then don’t touch it” is challenged with active participation and quick action. It is also beneficial here to define Kaizen not only as philosophy and mindset but also as a tool available to the Black Belt to utilize.
The most important part of the Kaizen event is a focus on the customer. This is done by seeking and identifying the Critical to Quality (CTQs) requirements and the core business process that enable these CTQs. Kaizen also must identify the “Ys”: the desired outcomes with a steadfast focus on the appropriate objective in measurable terms.
Another facet of Kaizen is that it is a set of tools that is based on the use of data and variation reduction tools kit including Statistics, Statistical Process Control (SPC), Project Management, Facilitation, and Team Management to achieve breakthrough results. These set of tools of quick change present itself at least at two points of the lifecycle of the transformation process: First after the project’s prioritization and secondly after Measure phase. (See Exhibit A and B). Kaizen shows its value after the Define phase and in the middle of DMAIC after concluding the Measure phase.
Kaizen has also been called Workout because it usually takes place in a structured 3-5 days facilitated meeting with Subject Matter Experts (SME) and Stakeholders. It is also called a Blitz because of its nature to identify quick wins realized within 5-10 days in contrast to the Define, Measure, Analyze, Improve and Control (DMAIC) process that could take up to 120 days.
Kaizen Implementation
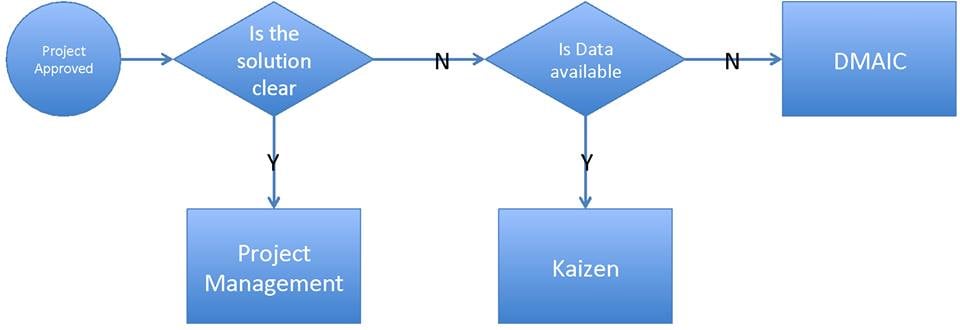
Exhibit A: Project Priority and Selection process - Lifecycle of Transformation effort
The first opportunity to utilize the Kaizen process is when the Solution is not clear to make a traditional project of it, however, there is a great deal of Data and insight to what the solution might look like.
While Kaizen activities include Project Management tools, it is far more complex due to its cross-functional and cross-departmental nature. Projects that have a clear objective statement are managed with a different approach and rigger. Kaizen events require an ongoing commitment to the Strategic objectives, the process and the customers of that process. Also, most of the time Kaizen events address efforts/projects where the solution is not clear or known to the SMEs. This means that it can’t be completed as typical project management of “just do it,” because Key input of SME’s is needed. And the project is cross-functional and cross-departmental in nature.
Kaizen presents itself as the tool of choice immediately after the Black Belt together with the Champion having a list of clearly defined projects to tackle. The lists of the project here have all the elements of Define including Business Case and Problem Statement that clearly describe the project. This clarity of the scope and project definition is critical to the success of the Kaizen/Workout/Blitz process.
The Second opportunity to utilize the Kaizen process is after the Measure phase in the DMAIC process. By this time, the team has been working on a weekly basis to identify Critical To Quality (CTQ) variables that are key input variable to the business opportunity or problem statements. And at the conclusion of the Measure phase and discovery of these measured variables, it became clear to the Black Belt with the team’s SMEs that there are actions that can be taken to harvest the low hanging fruits also called quick wins.
(See exhibit B): Recall that the DMAIC process of Lean Six Sigma usually address issues where we have a problem, however, we don’t know the solution or the solution is not clear for the Belt to execute. This is why the team spends a great deal of activates to define and measure and analyze the data before they can have a clear line of sight to the nature of the solution. However, most of the time after the Define and Measure phases a typical team would have compiled a collection of Metrics and Data related to the project. This brings visibility and insight that was not available at the beginning of the DMAIC process. As a result, the team now can see possible solutions to the charter being addressed.
It is more efficient not to wait till the end of the DMAIC process and present the Champion, SMEs and the Stakeholders of potential benefits that could be gained from this insight immediately. The opportunity for quick changing to the better becomes clear. This is where the call is for Kaizen.
How Kaizen works with DMAIC process
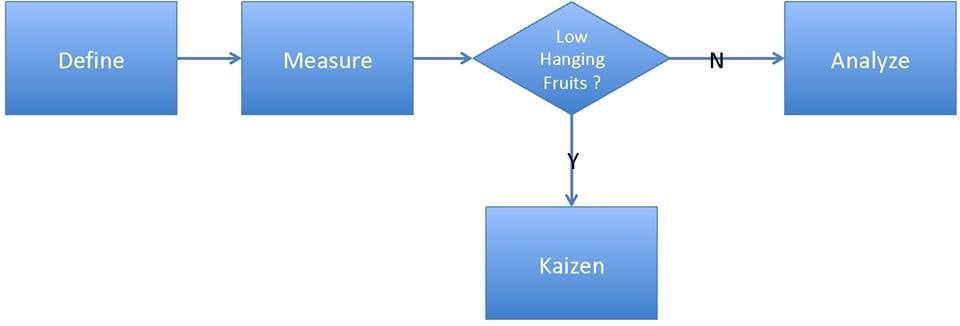
Exhibit B: DMAIC process with Kaizen touch points
Kaizen is also a process in the Continual Improvement effort. In order for the Kaizen event to be successful both Management sponsorship and Process area, SMEs must be mobilized and committed to each step of this effort. The process is rigorous and requires attention to details before, during and after the event.
Regardless of when the Kaizen event is being realized; it needs to have at minimum the following prerequisites elements before the event takes place:
- Clear Business Case and/or Opportunity statement
- List of SMEs to attend
- List of Stakeholders to be informed
- Clear Scope and desired outcome statement
- Value Stream Map with SIPOC
- Data, Metrics, and Findings
- All possible Risk identified and rated
- Detailed Agenda and Schedule of the Event
The Kaizen effort can be costly to the organization not only in opportunity cost (the SMEs could have been doing their daily jobs) but also in actual Labor cost. The average team meeting has about 12 members of the organization between Subject Matter Experts (SMEs) and Belts organization and facilitating the event. It is also important to add that most Kaizen events need to travel: While the majority of the SMEs are local, few need to travel to a localized place, which also adds to Lodging and Travel costs. This is why it is important to have a clear Business Case that would at least generate a Return of the time spent at the Kaizen event.
The Scope is the most critical factor in any meeting, let alone a Kaizen event. It is pivotal that the Belt has a sharply focused scope statement. In some cases, it is recommended not only to dictate what is in scope but also what is “out of scope.”
Given that the team has time constraints, the Belt must have done their homework prior to the event. To that end, it is critical that the Belt brings along the Value Stream Map (VSM), together with the Supplier, Input, Process, Output, and Customer (SIPOC) Map. These ‘before’ event list will assure the success of the Kaizen event and will clearly communicate the What, Who and Why for this process. It is also highly recommended that the following activities be completed before the event:
- Obtain and document feedback from key Stakeholders and Champion
- Train the SMEs on needed tools that will be utilized
- Obtain Battle Box
- Assure all needed equipment are prepared
- Reserve an additional War room for the parallel operation
During the Kaizen event the following activities are required to assure the maximum utilization of all SME’s and Stakeholders time:
- Conduct kick-off meeting
- Value Map the current process end to end
- Action plan created
- Objectives outlined
- Daily progress review held
- Risk Mitigation plan completed
- The future State process map is completed
- Standard Operation Procedures SOP completed
- Final presentation completed
- Communications and Training plans drafted
The Kaizen event itself is called “Workout” because of the amount of work being done in limited time constraints. One can deduce from the list mentioned earlier that a great deal of work will be covered during this effort.
After the Kaizen event the following activities are recommended:
- Walkthroughs are conducted with process area team
- Follow up with Future State process owner
- Updated Process Metrics, measure, and data
- To Do list follow up
- The final measure of controlled metrics evaluated
- Training and SOP verification
Conclusion
Kaizen can be called Good Change, not only because that is the exact translation to the Japanese name “Kai” Good, and “Zen” Change. Regardless of the name, the spirit of Kaizen implies its Japanize property, as it is the notion of changing the current state of operations to a new future state. Kaizen is not only philosophy and set of tools; it’s a process with key deliverables and activities that span before, during and after the Continual Process Improvement effort.
Looking for a Change? Get Lean Six Sigma Certified