Zero Defects In Quality Management
Introduction
Zero Defects is referred to as a philosophy, a mentality, or a movement. It aims to minimize the number of defects in manufactured products and services as much as possible. Let us understand the concept of Zero Defects.
What does the concept of zero defect mean?
Zero Defects is a term coined by Mr. Philip Crosby in his book “Absolutes of Quality Management”. It is a popular, highly regarded concept in quality management. Six Sigma has adopted it as one of its major theories. That said, the concept has also faced a fair degree of criticism.
Some argue that a state of zero defects simply cannot exist. Others have worked hard to prove the naysayers wrong. They have pointed out that “zero defects” in quality management does not literally mean perfection. Instead, it refers to a state where waste is eliminated, and defects are reduced. It means ensuring the highest quality standards in projects.
Let's begin by taking a look at Quality Management itself. Quality management ensures that an organization, product, or service is consistent. It has four main components. These include:
- quality planning,
- quality assurance,
- quality control and
- quality improvement.
Quality management talks about a set of procedures that ensures that the deliverables produced are "fit for purpose". At the very outset of laying out a Quality Management Process involves setting quality targets, which are agreed with the customer. Generally, the lesser the defects the better the quality. With this, you will understand the concept of Zero Defects in quality management
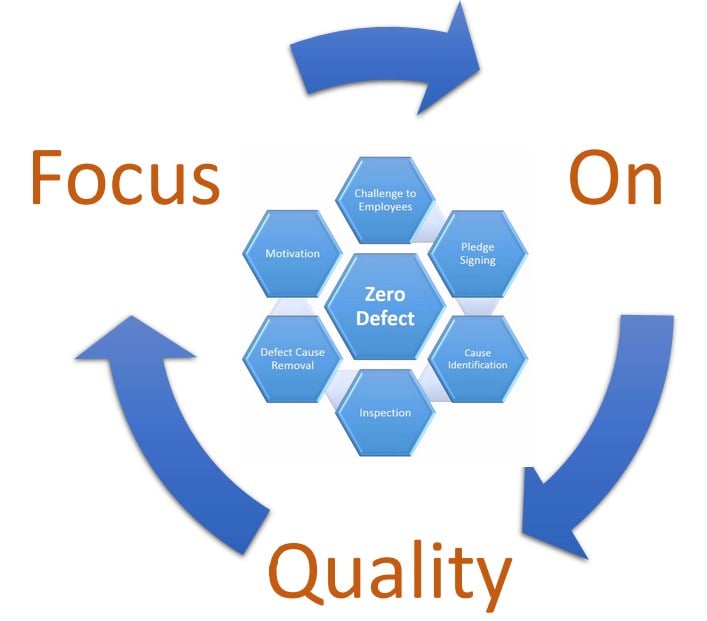
Relationship between zero defects and quality management
What Do We Mean by Zero Defects?
It is pretty obvious that attaining zero defects is technically not possible. Any sizable or complex manufacturing project will have some defects. The Six Sigma standard defines zero defects as 3.4 defects per million opportunities (DPMO). This allows for a 1.5-sigma process shift.
The zero defects concept is a quest for perfection to improve quality in the development or manufacturing process. True perfection might not be achievable. However, the quest will push quality and improvements to a point that is acceptable under even the most stringent metrics.
Let us take a quick look at DPMO. DPMO stands for defects per million opportunities. In process improvement efforts it is a measure of process performance. It is also known as nonconformities per million opportunities (NPMO).
A defect can be defined as a non-conformance of a quality characteristic to its specification. e.g. strength, width, response time. DPMO is stated in opportunities per million units for convenience. Some processes are considered highly capable (e.g., processes of Six Sigma quality). They experience only a handful of defects per million units produced (or services provided).
DPMO differs from reporting defective parts per million (PPM). It comprehends the possibility that a unit under inspection may be found to have multiple defects of the same type. It may also have multiple types of defects.
Identifying specific opportunities for defects (and therefore how to count and categorize defects) is an art. Generally, organizations consider the following when defining the number of opportunities per unit:
-
Knowledge of the process under study
-
Industry standards
-
When studying multiple types of defects, knowledge of the relative importance of each defect type in determining customer satisfaction
-
The time, effort, and cost to count and categorize defects in process output
Where is Zero Defects used?
Manufacturing organizations use it to tackle and improve quality issues. Zero Defects is referred to as a philosophy, a mentality, or a movement. It aims to minimize the number of defects in manufactured products and services as much as possible. It does not have distinct steps or rules to follow.
This leaves companies open to customizing how they want it to work for themselves. This is perhaps why Zero Defects can be so effective- it is adaptable to any situation, business, profession, or industry. It is used in Six Sigma for reducing the variation and standard deviation. This indirectly will reduce the defects and bring it close to zero.
Zero Defect Manufacturing Implementation
Today, apart from physical review and testing, we have machine learning, AI, IOT etc. These will help improve quality and eliminate many defects. Triggering factors could fall into two categories :
- Detection : Testing and review are carried out and defective products are repaired if possible.
- Prevention : Investigations take place to uncover process variations and how to improve upon the processes or resolve the unintended deviation thereof.
Principles of Zero Defects
According to Philip Crosby, the principles of Zero Defects are as follows:
Quality is the conformance to requirements:
Every product or service has a requirement. It is a description of what the customer expects to see. Hence, a certain product is said to have achieved quality when it meets those requirements. This should not be confused with higher standards of products. For instance, it will be unrealistic to say that a basic mobile phone is of low quality compared to the latest iPhone.
They both must meet different quality standards to pass the quality test. Based on this, Zero Defects means the basic mobile phone is a quality product if it meets the initial requirements set for it. That is, if it can make and take phone calls clearly, send and receive text messages. Then it is only realistic to say it conforms to quality and has (close to) Zero Defects.
Preventing defects is better than quality Inspection and Correction:
The focus is on product quality management here. It is preferable that defect prevention is made a part of manufacturing or company practice. It should be in the process rather than in quality inspection and correction. This is simply because Zero Defects management is almost always less troublesome. It is more certain, and less expensive, as it aims to prevent defects rather than to discover and correct them later.
Quality Standards Means Zero Defects:
The third principle of Zero Defects is based on the nature of requirements. A requirement expresses what is genuinely needed by the customer or the product itself. Any product or service unit that does not meet the requirements will not satisfy the need and is nowhere near as good as expected. Yet, in some cases, some units that do not meet requirements could still satisfy the need. This means the requirement should be reviewed and changed to reflect reality.
Quality Is Measured in Terms of Money (i.e. The Price of Non-conformance (PONC)):
Philip Crosby believes that every defect represents a hidden cost. This includes the costs of inspection time, reworking, and revenue. Furthermore, there is the cost of wasted material, labor, and customer dissatisfaction. When properly identified and brought to light, the effects of these costs can be made clear.
This will help provide a cost justification for steps to improve quality. Businesses should find a way to measure a Zero Defects management progress. This will help maintain management commitment, rewarding employees, and ensuring company goals are made measurable. With this, the actions can be made concrete. It will also help in making decisions based on relative returns.
Zero Defects – The Theory and Implementation
Zero Defects theory ensures that there is no waste existing in a project. Waste refers to all unproductive processes, tools, employees, and so on. It eliminates anything that is unproductive and does not add value to a project. This is called the process of elimination of waste. Eliminating waste creates a process of improvement and lowers costs.
“Doing it right the first time”, is common with the zero defects theory. This helps to avoid costly and time-consuming fixes later in the project management process.
The zero defects theory is based on four elements for implementation in real projects. Quality is a state of assurance to requirements. Therefore, Zero Defects in a project mean fulfilling requirements at that point in time. Right the first time. Quality should be integrated into the process from the beginning.
We should not be solving problems at a later stage. Quality is measured in financial terms. One needs to judge waste, production, and revenue in terms of budgetary impact. Performance should be judged by the accepted standards. It should be as close to perfection as possible.
Pros and Cons of zero defects concept
The clear advantage of achieving a zero-defect level is the stark reduction in wastage and costs. Zero defects mean higher customer satisfaction and improved customer loyalty. This invariably leads to better sales and profits.
A Zero Defects goal could lead to a scenario where a team is striving for a perfect process that cannot realistically be met. The time and resources dedicated to reaching Zero Defects may negatively impact performance. It can put a strain on employee morale and satisfaction. There can also be negative implications when you consider the full supply chain. Other manufacturers might have a different definition of Zero Defects.
In the end, the quest for Zero Defects is an admirable objective in itself. Most companies find that the pros outweigh the cons. Companies strive for stringent but accepted standards of defects. With this, companies can build better processes. It creates an environment that facilitates continuous service improvement.
Conclusion
It is technically not possible to have no defects. However, an acceptable quality level can be determined for the products and services. This level is determined on the basis of quality goals and customer requirements. We need to measure quality in financial terms. Measure the cost of conformance and non-conformance to quality.
Become a certified Lean Six Sigma Green and Black Belt holder with us!